We see value in waste
- Copy
The sirens of climate change are getting louder and the only possible response is sustainable development. Limiting the use of natural resources through innovative environment-related solutions is a critical need for industry.
At the Aditya Birla Group, we believe that a sustainable world necessitates building sustainable businesses. Such businesses must operate successfully within the progressively tougher legal standards and tighter resource constraints that will become a reality over time.
Our businesses are taking proactive measures to fulfil our vision of becoming the leading Indian conglomerate for sustainable business practices across our global operations. One significant area is the movement towards a circular economy by managing waste for a cleaner, more environment-friendly manufacturing process.
Waste management is part of the Group’s sustainable business framework. And a circular economy is based on the principle of using a few resources judiciously, deriving the complete value out of them and, once the material is fully degraded, recycling it into another form.
Collaborative approach
Hindalco's approach of managing the red mud generated from alumina refining is a great example of how one industry's waste can be a raw material for another, leading to environmental advantages like conserving virgin minerals and land, reducing air emissions, while simultaneously reducing costs. Over the past five years, Hindalco has invested intensive R&D efforts to identify a permanent solution for the disposal of bauxite residue; one that can be used by the aluminium industry worldwide.
Two of our flagships, Hindalco Industries Ltd and UltraTech Cement Ltd have joined hands to promote a circular economy. Hindalco has recently entered a memorandum of understanding (MoU) with India’s largest cement and concrete manufacturer, UltraTech Cement, to supply 1.2 million tonnes of bauxite residue or red mud per annum to 14 UltraTech plants located in seven states.
With this, Hindalco has become the first company in the world to utilise 100 per cent of the red mud generated in the alumina manufacturing process across three of its refineries. Towards this, Hindalco supplies 250,000 tonnes of bauxite residue per month to 40 cement companies, and the goal is to scale up utilisation to 2.5 million tonnes over the next few years. The domestic aluminium industry generates 8-10 million tonnes of bauxite residue annually and if every cement company in India starts using red mud, the challenge of storing red mud will no longer exist. On its part, Hindalco is investing to ensure that this sustainable solution gets widespread acceptance, and providing logistics support to transport red mud to cement plants in different states across India.
Value in waste
Red mud is rich in iron oxides, alumina, silica and alkali. The residue is typically stored on large tracts of land, which poses an environmental challenge. However, the cement industry has developed the capability to process red mud as a replacement for mined minerals such as laterite and lithomarge.
Hindalco has also received a patent for manufacturing red mud bricks by the Patent Office of India. The product innovation uses 70% process waste, comprising largely of red mud, fly ash and bottom ash. The bricks have application in the construction sector for walls, floors and other uses. The red mud brick initiative is an example of Hindalco's Sustainable Business Model as it creates value out of a manufacturing by-product, exemplifies the circular economy model where waste from one industry is used as an input for another.
The red mud brick formulation was designed at the Company's integrated aluminium complex in Renukoot, Uttar Pradesh, and provides a sustainable alternative to fired-clay bricks.
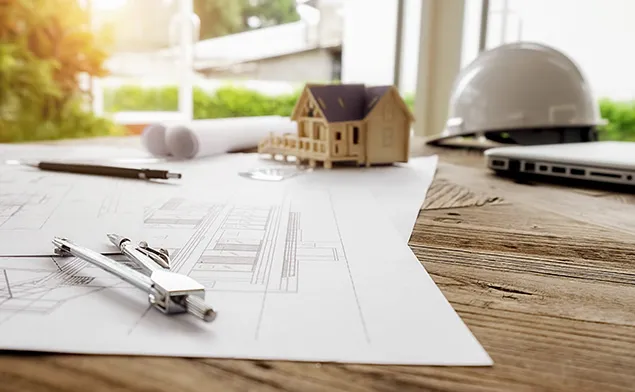
Sustainable manufacturing
By using the red mud supplied by Hindalco as an effective substitute for mined minerals, UltraTech has successfully replaced up to 3 per cent of its clinker raw mix volume. In the process, it has reduced its dependence on natural resources.
Going forward, with an annual supply of 1.2 million metric tonnes of red mud from Hindalco, the company expects to conserve more than one million tonne of mined natural resources like laterite in its manufacturing process. Thus, the innovative use of red mud has resulted in a win-win situation for both Hindalco and UltraTech – while achieving significant sustainability goals.
Apart from red mud, UltraTech also utilises fly ash, a by-product from coal-fired power stations and slag as clinker replacement. In 2019 alone, UltraTech utilised more than 15 million tonnes of industrial waste material as an alternative raw material for cement production.
UltraTech also uses industrial by-products and municipal waste as an alternative fuel source used to fire the kilns. Untreated municipal waste emits greenhouse gases and can contaminate soil and water resources, affecting human health and the environment. Disposal of this waste in landfills requires large parcels of land and entails high cost of construction and operation.
Waste as fuel
By co-processing municipal solid waste, UltraTech offers a perfect alternative to land-filling and incineration of waste. The company currently co-processes over 360,000 tonnes of industrial and municipal solid waste, including 146,426 tonnes of non-recyclable plastic waste every year as an alternative fuel in its kilns.
The company also ensures the use of environment-friendly processes. For instance, the pollutants are completely destroyed because of high combustion temperatures. There is no residual waste as the combustion ash is integrated into the clinker, and there are no emissions either. The quality of cement produced remains of the highest standard.
UltraTech has tied up with municipal corporations across Rajasthan, Tamil Nadu, Karnataka, Gujarat and Andhra Pradesh to eliminate non-biodegradable municipal waste in a safe and sustainable manner.
Sustained Sustainability
UltraTech has extended the adoption of circularity philosophy also in its upstream concrete business. The company has commissioned the world’s first zero discharge ready mix concrete (RMC) plant, i.e. with no discharge of liquid or solid waste in 2019. The company achieved this by developing in-house an automated technology for recycling all the waste sludge or slurry generated from rejected concrete into producing RMC. This innovation has significant benefits of reducing the impact on environment as well as conservation of resources.
By innovating new ways of managing waste, Aditya Birla Group is converting waste into a resource and moving towards a cleaner process of manufacturing and in turn generating value for the society. More important, this future-proofing strategy helps exponentially increase the sustainability quotient of the Group.
Mr. Sandeep Gurumurthi
Group Head, Communication & Brand
Aditya Birla Management Corporation Pvt. Ltd.
Call: +91-22-6652-5000 / 2499-5000
Fax: +91-22-6652-5741 / 42