Why 'Car to Car' is a Sustainable Auto Solution
- Copy
What makes Novelis’ aluminium a much-in-demand metal in the automotive sector? Used by top brands worldwide and present in more than 225 models on the road? The answer lies beyond the aluminium-maker’s innovative alloys, global manufacturing footprint, and ability to deliver consistent quality at scale. It’s about how Novelis makes automotive aluminium a sustainable metal that helps vehicle manufacturers and consumers to reduce their carbon footprint.
Over the years, Novelis has partnered with many automotive makers to give shape to the world's most environment-friendly cars. One of the ways it does this is by increasing focus on recycling aluminium in order to minimise its use of primary, newly mined aluminium.
Novelis also actively partners with the automotive industry to move toward a lower-carbon and increasingly circular business model. The US-based company has pioneered a closed-loop recycling (CLR) system that takes aluminium scrap generated via auto makers’ manufacturing steps, reforms it into the same grade of metal and inserts it back into the supply chain for its customers.
“Closed-loop recycling allows us to take back as much of our customers’ aluminium scrap as possible, turning it directly back into the same product again,” explains Pierre Labat, Vice President, Global Automotive Sales and Marketing for Novelis.
The benefits of closed-loop manufacturing are many. Novelis' closed-loop recycling process recycles aluminium on a large scale, saving over 90 percent of the energy that would otherwise be consumed to create virgin raw material. That is a huge reduction on energy use and carbon emissions.
Closing the loop also preserves the value of the alloy, reduces recycling and transportation costs, minimises the environmental impact and establishes a secure supply chain. In addition, closed-loop recycling provides value to customers, mainly by helping them meet their sustainability objectives and increase post-consumer recycling of aluminium. “We help our customers make sustainable products that consumers want,” says Mr. Labat.
Here’s the story of how Novelis' collaboration with Jaguar Land Rover (JLR) in 2013 paved the way for the automotive sector to embrace closed-loop recycling initiatives.
The JLR-Novelis Partnership
JLR wished to mitigate the energy and cost-intensive nature of using primary aluminium in the production process. It turned to its long-standing partner Novelis for a high-recycled content material solution.
In a traditional manufacturing environment, an estimated 30-40 percent of the automotive sheet is left over after a manufacturing plant stamps out automotive parts. To preserve the value of this surplus material, Novelis and JLR needed to streamline the material supply chain to reduce the total carbon footprint of the entire automotive production cycle.
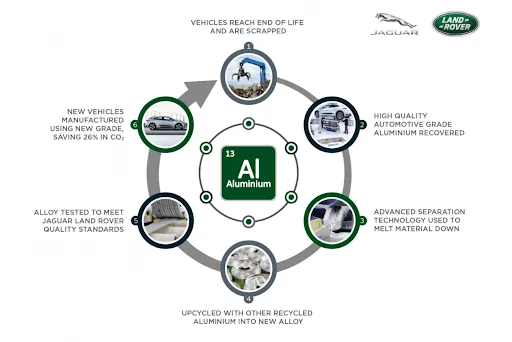
(Source: https://www.jaguarlandrover.com/news/2020/08/jaguar-land-rover-upcycles-aluminium-cut-carbon-emissions-quarter)
Accordingly, the companies implemented a closed-loop recycling system, at the core of which was the development of an aluminium alloy. The alloy needed to meet the high-recycled content threshold requirement while also delivering the strength, durability, and formability specified by JLR's engineers.
As part of the implementation plan, Novelis created a new alloy — Novelis Advanz™ 5F-s5754 RC, containing at least 75 percent recycled content. First introduced in the new Jaguar XE, this alloy is now featured in all new and legacy Jaguar Land Rover models. As the automotive industry evolves toward a fully closed-loop recycling model, the alloy could ultimately contain up to 100 percent recycled content from automotive scrap.
This process has resulted in more than $1 million in savings to date and an 80 percent reduction in CO2 equivalent emissions than standard road transport.
The alloy is an integral part of JLR’s REALCAR (REcycled ALuminium CAR) project, an award-winning, multi-stakeholder initiative established in 2008 to create a closed-loop vehicle production model that recycles end-life automobile scrap. Since 2013, JLR has collected and reused about 300,000 metric tons of aluminium.
Together, Novelis and JLR won the prestigious European Aluminium Award for their automotive aluminium innovations and closed-loop recycling system.
The word spreads
Following the success of Novelis’ closed-loop recycling initiative with JLR, other automotive manufacturers embraced the process. In North America, Novelis and Ford developed the world’s largest closed-loop recycling system for the automaker’s most popular line of aluminium-intensive trucks – the F-150. Through the programme, Ford recycles and reuses more than 90 percent of scrap, enough to produce 30,000 F-150 truck bodies each month.
Audi, BMW and Volvo followed suit, inking partnerships with Novelis for closed-loop recycling systems in Europe. Nissan has also embraced closed-loop recycling and recently rolled out units of the all-new 2021 Nissan Rogue, its first global model to operate under this type of system. After implementing the system in the USA, Nissan will follow up with a new closed-loop recycling system in the UK later this year, becoming Novelis' first customer with a multi-region closed-loop recycling programme.
Nissan's system will help in reducing CO2 emissions when compared with using parts made with primary alloys from virgin raw materials. The new system has reduced dependence on newly mined resources and lowers waste generation in its factories.
As the world’s largest aluminium recycler, Novelis is leveraging aluminium's unique properties to deliver sustainable solutions that help the automobile industry appeal to customers, meet government regulations, reduce environmental impact and drive cost efficiencies. That’s an all-round winning solution.
Mr. Sandeep Gurumurthi
Group Head, Communication & Brand
Aditya Birla Management Corporation Pvt. Ltd.
Call: +91-22-6652-5000 / 2499-5000
Fax: +91-22-6652-5741 / 42